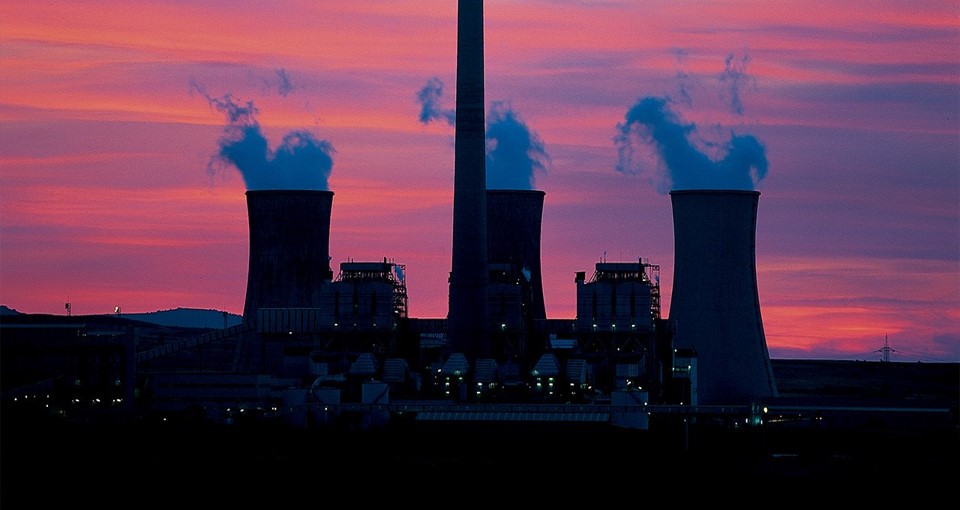
IS THE ANTISTATIC PROTECTION REALLY NECESSARY?
The antistatic behaviour on a garment is needed for different final applications.
In the oil and gas, or basically all the companies that have an ATEX area, the antistatic behaviour is needed to avoid the possible sparks that could occur in such environments, which could cause sudden fire and explosion, which in the worst cases could result in even the death of the workers in the area.
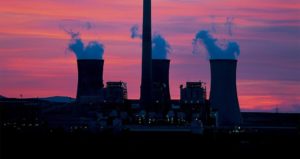
Antistatic Behaviour
Another workplace where the antistatic behaviour is needed is the manipulation of electronic components, where the static electricity would cause the malfunction of the device or the painting rooms, where the antistatic behaviour is needed to have a homogeneous spread of the paint.
The EN 1149-5 specifies requirements for materials and design of protective clothing with electrostatic dissipation, used as part of a complete set grounded to avoid incendiary discharges.
An electrostatic dissipating garment must meet at least one of the following requirements:
- t50 < 4s or S > 0.2 tested according to EN 1149-3 Method 2 (induction charging).
- surface resistance equal to or less than 2.5 x 109 Ω in at least one of the surfaces tested according to the norm EN 1149-1.
For the fabric, which is the material that will give to the garment the antistatic properties, there are 3 different regulations, and as explained above, depending on the final use there is needed to pass at least one of them:
UNE EN 1149-1: Electrostatic properties. Surface resistivity
This test method is not applicable to fabrics with conductive fibre core. The sample is placed on an insulating base plate, then the electrodes are placed on the sample, and a continuous stream is applied. Then the resistance of the sample is measured.
Requirements: the surface resistivity must be less than 5 x 1010 Ω.
This is the regulation needed for painting rooms.
UNE EN 1149-2: Electrostatic properties. Test methods for measurement of the electrical resistance through a material (vertical resistance)
This standard does not apply to specify the protection against electrical stresses.
The electrodes are placed on opposite surface of the test material. Then a DC voltage is applied to the electrodes and determine the electrical resistance of the tested material.
This test is performed to pass the EN 11611, which is the PPE that will be used for welding purposes.
UNE EN 1149-3: Electrostatic properties. Test methods for measurement of charge decay
The charge of the test sample is performed by inductive effect. Below the test sample, which remains in horizontal position, an electrode is placed. The electrode is with no contact with the test sample. The electrode is suddenly brought to a high voltage. If the sample is conductive or contain conductive elements, it’s induced on it a charge with opposite sign to the electrode. This effect is measured and recorded behind of the sample with an appropriate probe, and is used to determine the time of semi-dissipation (t50) and protection coefficient (S).
This is the regulation needed in PPE where there is an ATEX zone.